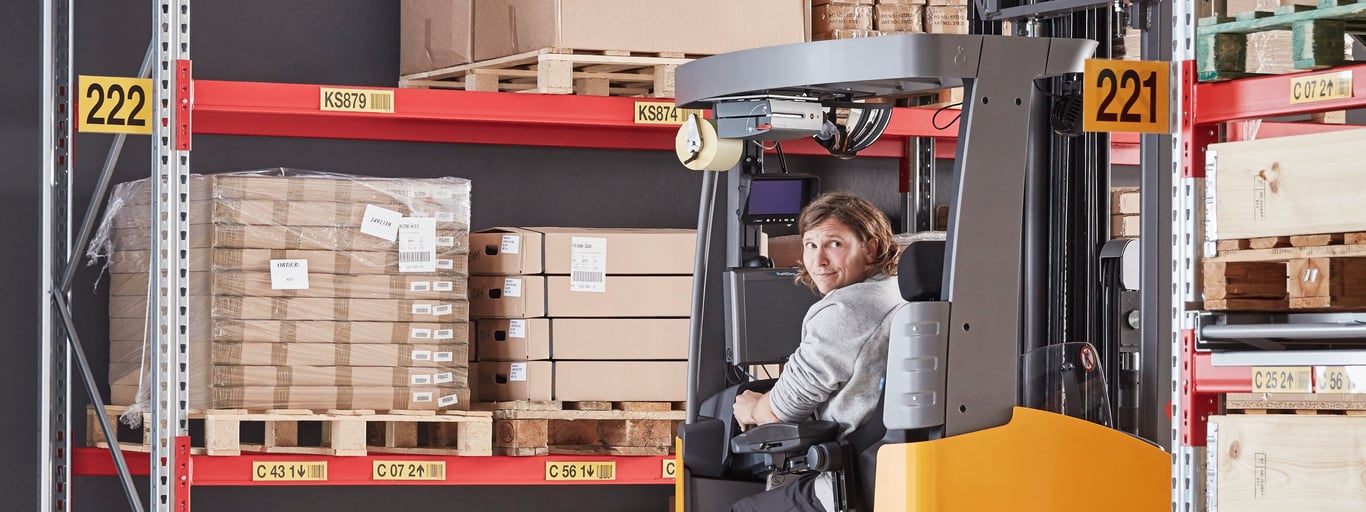
Four benefits of efficient logistics flow
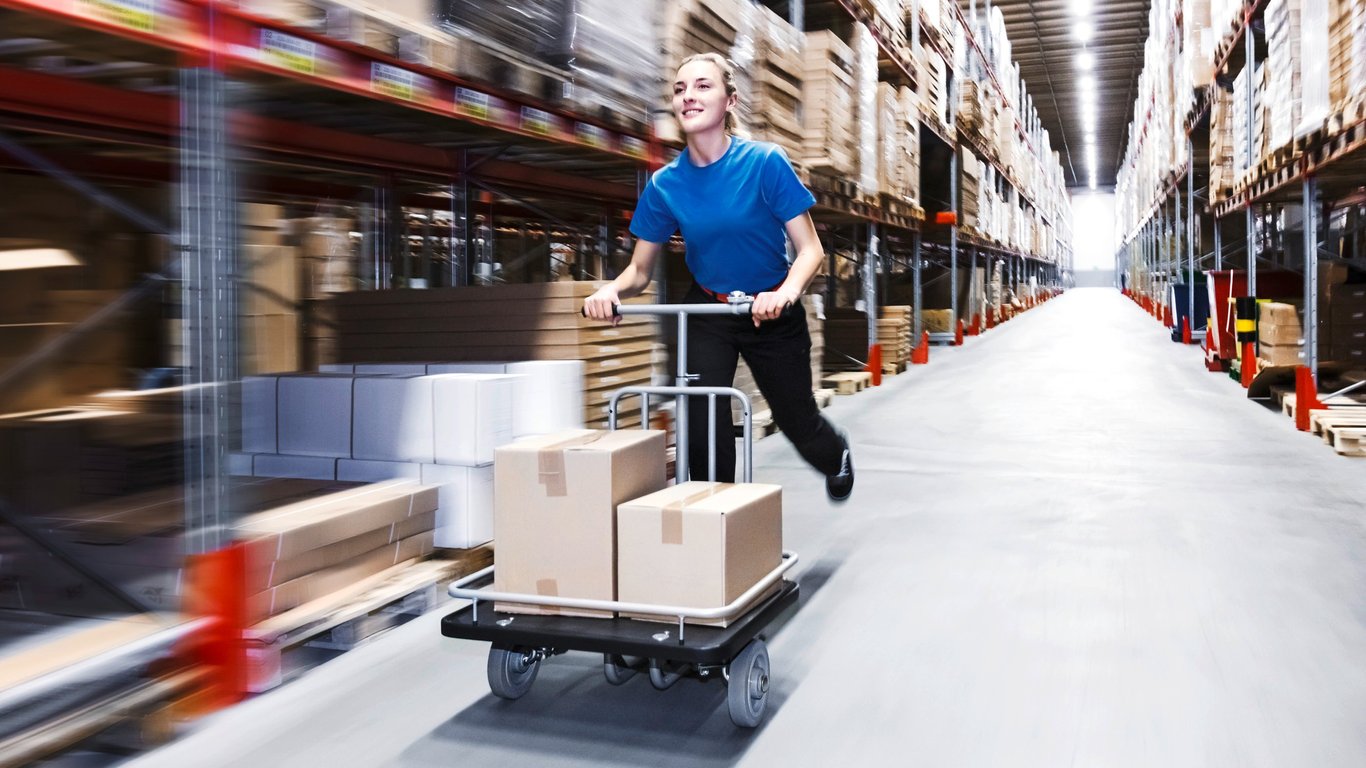
1. Time is put to better use
It is impossible to create extra hours in the day but it is easy to use working time in the warehouse more efficiently. For example, by minimising time-intensive procedures such as unnecessarily long journeys from where an item is picked to where it is despatched, cumbersome picking routines and queues at packing stations. What's needed is careful planning about where in the warehouse high- and low-volume items are stored so that the most popular goods can be picked more quickly. It’s also essential to give staff the best possible tools to do their job most efficiently, whether that’s more picking trolleys or better equipped packing tables.
Once the right processes in place, customers, managers and workers will all start to see results they are satisfied with.
2. Employees stay healthy
Healthy and motivated employees are essential for an efficient warehouse. So investing in constant improvement from the outset is important. Here's the thing: poor managed workflows often result in a shortage of time and more stress for staff. This in turn can lead to errors in picking and handling, which affects the service provided to customers. It can also lead to injuries, sick leave and employees choosing to quit, so that new or temporary staff must be brought in and trained - which is both time-consuming and costly.
The solution is to invest in a good work environment, where well-being as well as ergonomics, safety and smart routines are prioritised. The positive impact of these investments won’t take long to show.
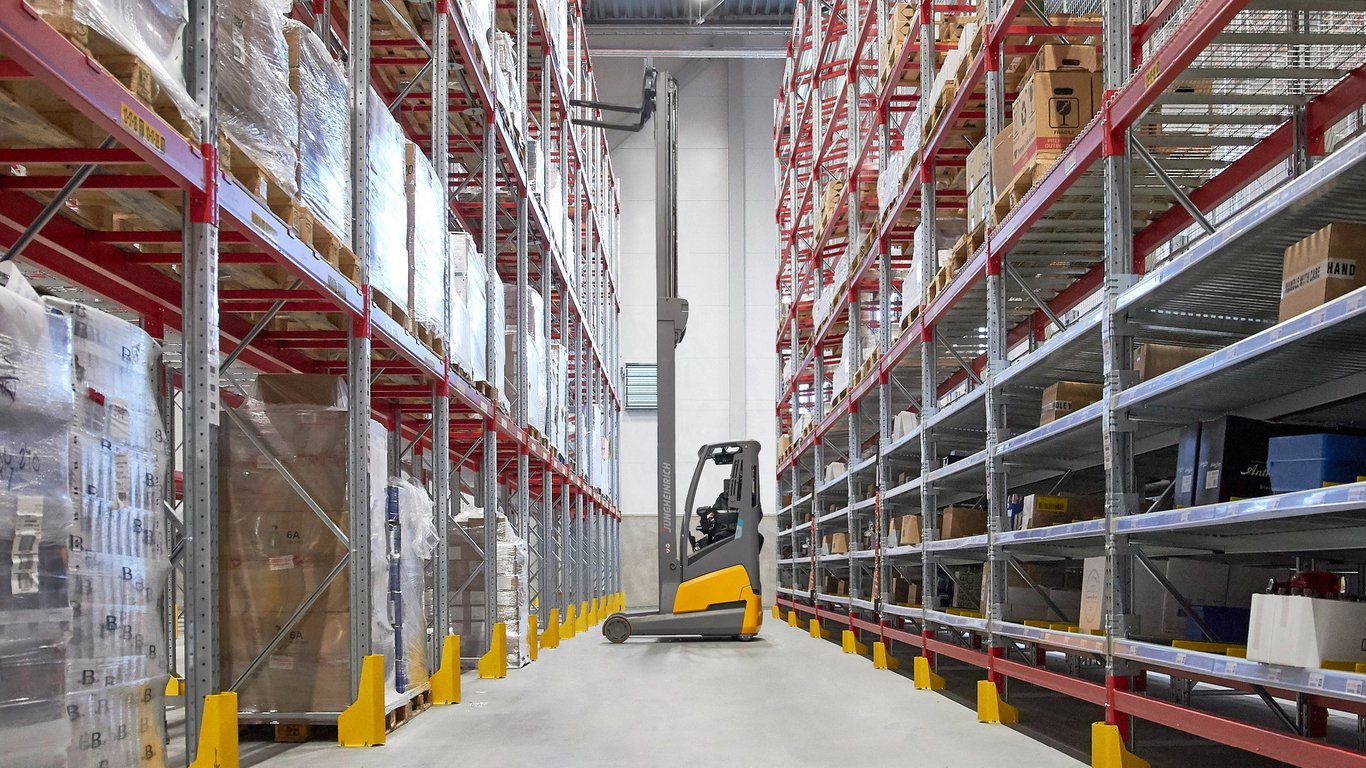
3. The cost of premises can be kept down
Warehouse optimisation is a smart way to maximise load capacity in a given area. By adapting shelving and pallet racking to the nature of the goods and the dimensions of the premises, the need for an extension or possible relocation (with associated costs) can be avoided. So how much capacity must the warehouse have? Do not fit out the space around seasonal peaks such as Black Week and Christmas, when you risk being left with excess capacity and empty shelves for the rest of the year. Ideally, your warehouse should be designed to cope with normal demand and be kept 80-85% full at all times. The business should then plan to make use of an overflow warehouse for limited time periods if necessary to meet peak demand.
That said, there's a limit to when the use of external help costs more than it's worth, and the argument for expanding your own warehouse begins to gain traction. This will depend on how much the volume increases at peak times and how sustained it is. If it’s more than a few weeks a year then it may be time to expand your premises. It's all a question of what will be best in the long run to keep the business running efficiently.
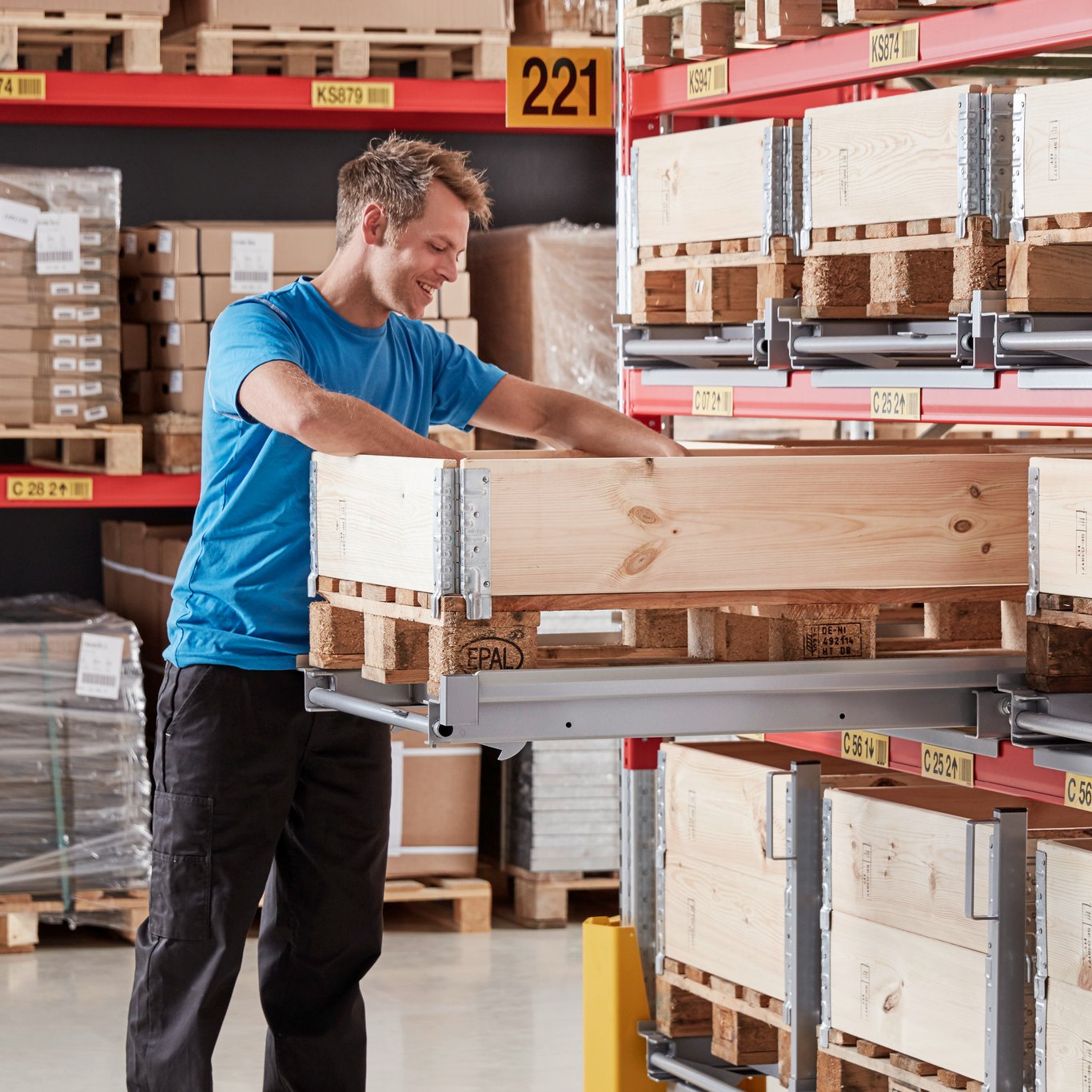
4. Customers are happy to return
Why ramp up stock flow? Because warehouse performance has a major impact on customer experience. The warehouse is an important part of the chain, which also consists of choice of goods, supply, marketing and sales. When all the parts of the chain work together and click seamlessly into place, the criteria for a good, lasting relationship with the customer are in place.
In a warehouse with a well-thought-out floor plan, well-balanced capacity and the right type of equipment, it's easy for employees to do a good job. The goods are there on site and can be picked, packed and despatched immediately, which means that customers are satisfied and happy to use you again and again.